The Importance of Tooling Mold in Metal Fabrication
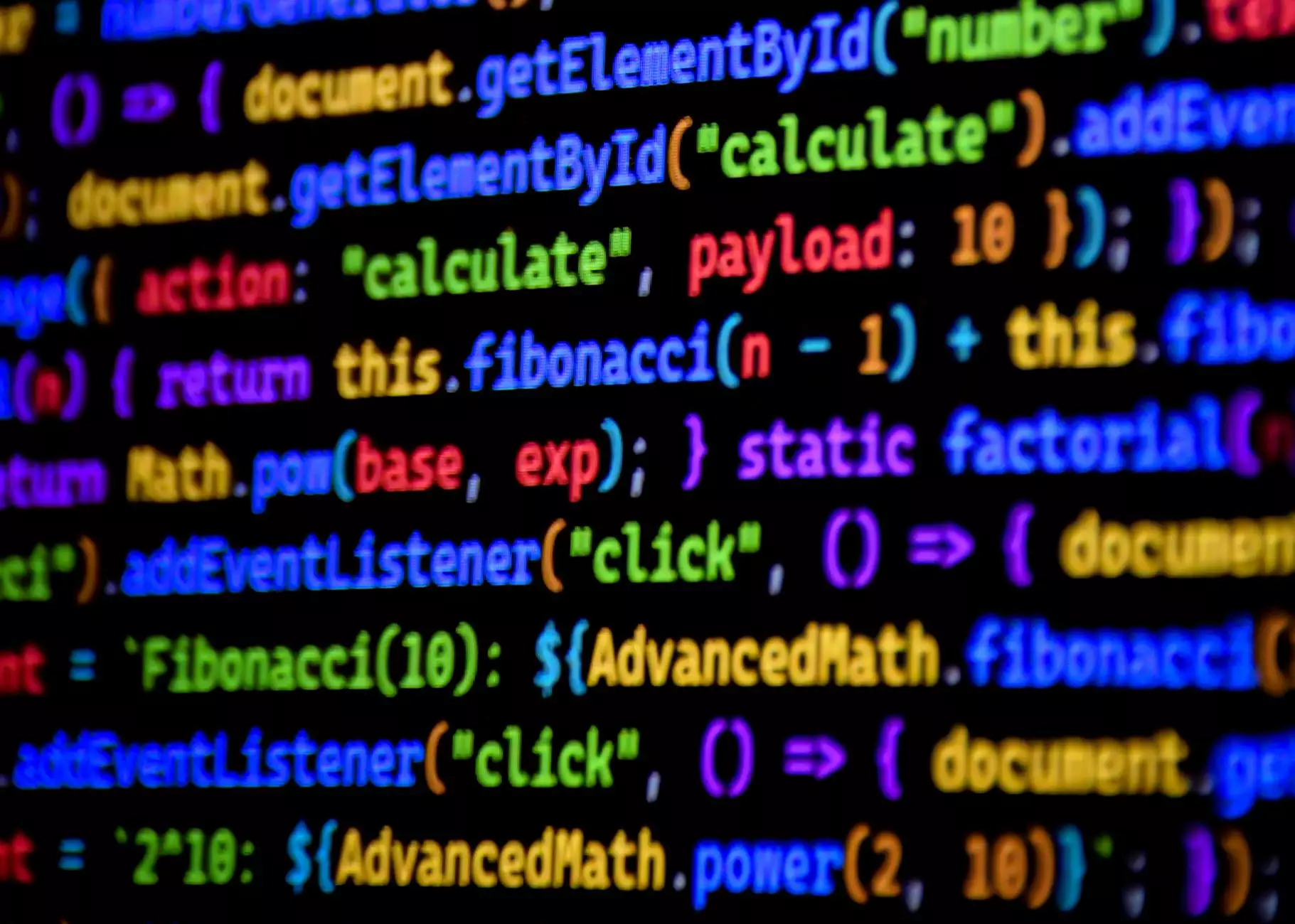
In the ever-evolving landscape of manufacturing, tooling mold has emerged as a linchpin in the production of high-quality metal products. As businesses strive for efficiency and precision, the role of tooling molds has become increasingly crucial. This article delves deep into the intricacies of tooling molds, their applications, benefits, and the impact they have on the metal fabrication industry.
What is Tooling Mold?
Tooling mold refers to the various tools and dies used to shape and form materials during the manufacturing process. These molds serve as templates for creating components with consistent dimensions and quality. In the context of metal fabrication, a tooling mold can be made from various materials, including steel, aluminum, and even plastic, depending on the specific application.
Types of Tooling Molds
Understanding the various types of tooling molds is essential for grasping their applications in metal fabrication. Here are the most common types:
- Injection Molds: Used for creating parts by injecting molten material into a mold cavity.
- Blow Molds: Employed for hollow parts, these molds utilize air pressure to form shapes.
- Compression Molds: These molds are primarily used for shaping thermosetting plastics.
- Die Casting Molds: Used to produce intricate metal components by pouring molten metal into a mold.
- Extrusion Molds: These molds create continuous shapes by forcing material through a shaped opening.
The Role of Tooling Mold in Metal Fabrication
Tooling molds play a transformative role in metal fabrication. They are not merely tools but integral components of the production process, ensuring that the highest standards of quality and efficiency are met. Let’s explore how tooling molds influence metal fabrication:
1. Consistency and Precision
One of the primary advantages of using tooling molds is the ability to produce components with consistent dimensions and specifications. This is particularly important in industries where precision is critical, such as aerospace and automotive manufacturing. Tooling molds give manufacturers the ability to replicate components accurately, minimizing variances that can occur during manual production processes.
2. Reduced Lead Time
The implementation of tooling molds can significantly reduce the lead time in production cycles. When molds are pre-designed and manufactured, they streamline the production process. This efficiency allows businesses to respond quicker to market demands, which is an essential factor in today’s fast-paced business environment.
3. Cost Efficiency
While the initial investment in tooling molds can be substantial, the long-term savings they provide make them cost-effective. By producing parts in bulk with molds, companies can reduce material waste and labor costs. Furthermore, automation often accompanies the use of tooling molds, which further decreases operational expenses over time.
4. Design Flexibility
Tooling molds allow for a great deal of design flexibility. Engineers and designers can experiment with different shapes and sizes without the extensive retooling that manual processes often require. This flexibility fosters innovation, enabling businesses to bring new products to market more efficiently.
Factors Influencing Tooling Mold Design
The design of a tooling mold is influenced by various factors, including:
- Material Type: Different materials require unique mold designs and considerations to ensure the final product meets quality standards.
- Production Volume: The expected volume of production can dictate whether a long-lasting or a short-term mold is needed.
- Component Complexity: Complex components may require more sophisticated mold designs to replicate intricate details accurately.
- Budget Constraints: The financial resources available can limit the technologies and materials used in mold creation.
Main Applications of Tooling Mold
Tooling molds find applications across a plethora of industries. Here are some of the key areas where they are extensively utilized:
Aerospace Industry
The aerospace industry demands components that adhere to rigorous safety and quality standards. Tooling molds ensure the precision and reliability needed for aircraft components, from engine parts to interior fittings.
Automotive Manufacturing
In automotive production, molds are crucial for creating parts such as dashboards, bumpers, and body panels. Tooling molds facilitate the mass production of automotive components while ensuring they meet safety and performance standards.
Consumer Electronics
With the rapid development of consumer electronics, tooling molds allow manufacturers to produce intricate parts for devices quickly and cost-effectively. From smartphone casings to circuit boards, the quality replication of components is vital for maintaining competitiveness in this market.
Medical Devices
Precision is paramount in the medical industry. Tooling molds are used to fabricate medical devices that require strict adherence to quality regulations, ensuring patient safety and device efficacy.
Best Practices for Tooling Mold Maintenance
To maximize the lifespan and performance of tooling molds, best practices for maintenance should be observed. These include:
- Regular Inspection: Conduct frequent checks for wear and tear to avoid costly downtime.
- Proper Cleaning: Clean molds regularly to remove debris and residues that can affect quality.
- Lubrication: Ensure that moving parts are well-lubricated to prevent damage and wear.
- Calibration: Periodically calibrate molds to maintain precision and alignment.
Future Trends in Tooling Mold Technology
As technology advances, so does the field of tooling molds. Several emerging trends are shaping the future of this integral manufacturing component:
1. 3D Printing Technology
3D printing is revolutionizing how molds are designed and produced. Rapid prototyping allows for quick iterations in design, making it easier to test and optimize tooling molds before full-scale production.
2. Smart Manufacturing
The integration of IoT (Internet of Things) technology into tooling mold processes facilitates data collection and analysis that can lead to enhanced efficiency and predictive maintenance. Smart molds will be able to communicate their status and performance metrics to reduce downtime.
3. Sustainable Materials
As sustainability becomes a priority across all industries, there is a growing trend towards using more eco-friendly materials for tooling molds. Companies are looking for ways to reduce their carbon footprint while still maintaining the quality and performance of their molds.
Conclusion
The significance of tooling mold in the metal fabrication industry cannot be overstated. They play a vital role in ensuring efficiency, precision, and quality in manufacturing processes. As industries continue to evolve, adopting cutting-edge technologies and practices, tooling molds will remain the backbone of innovative production strategies.
For businesses invested in metal fabrication, understanding and optimizing tooling mold usage could be the key to unlocking new market opportunities and maintaining a competitive edge. As we embrace future trends like 3D printing and smart manufacturing, it is evident that the realm of tooling molds will continue to flourish, providing immense benefits to manufacturers across the globe.