Understanding the Importance of H2S Monitor Calibration
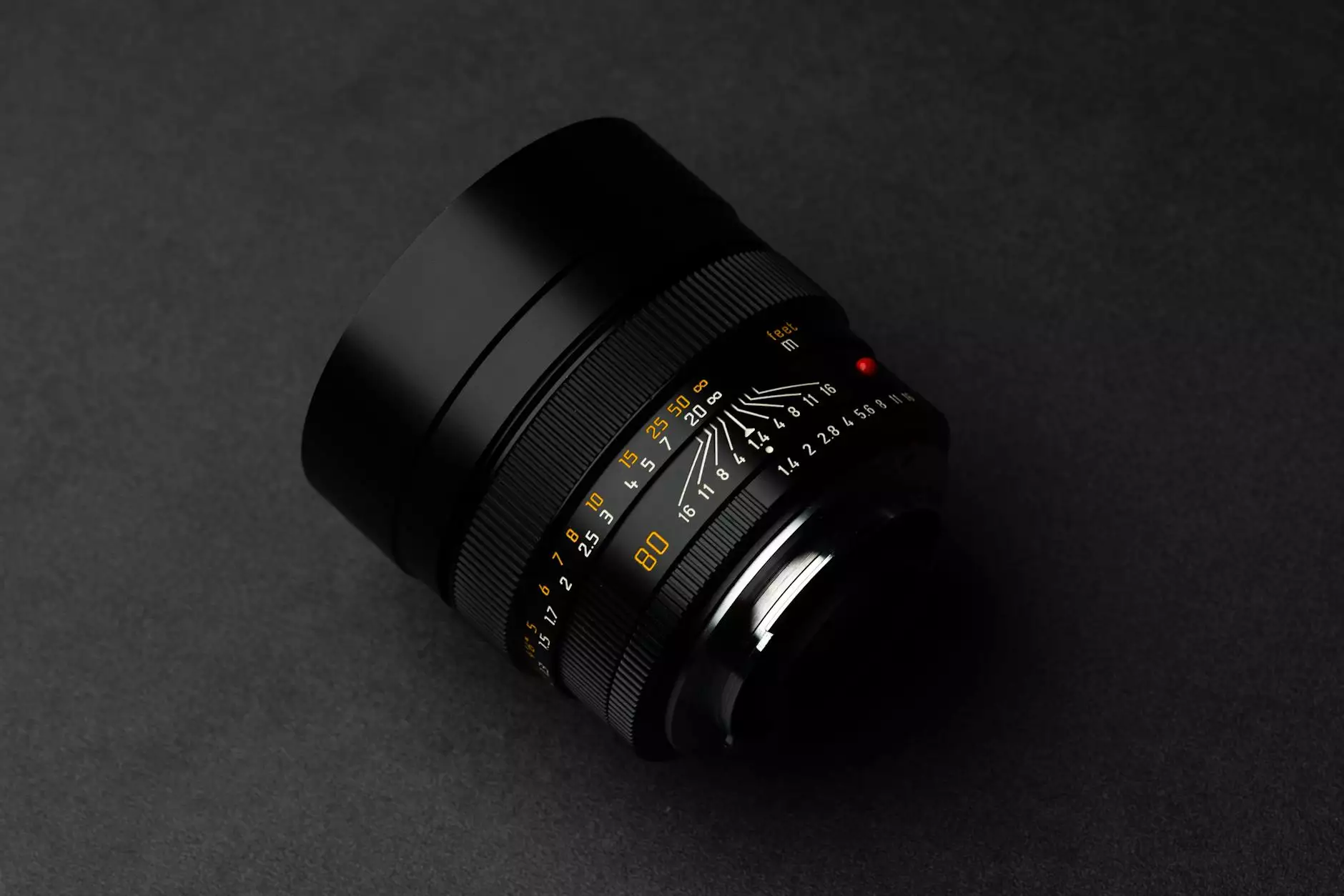
Hydrogen Sulfide (H2S) is a highly dangerous gas that can pose serious health risks to workers in various industries, particularly in sectors such as oil and gas, wastewater treatment, and agriculture. The use of H2S monitors is critical to ensure that employees are protected from exposure to this toxic gas. However, for these monitors to function effectively, regular H2S monitor calibration is essential.
What is H2S Monitor Calibration?
H2S monitor calibration is the process of adjusting and verifying the accuracy of hydrogen sulfide detectors to ensure they provide reliable measurements of gas concentrations in the atmosphere. This process involves testing the monitor’s response to known concentrations of H2S and adjusting the readings as necessary.
The Importance of Regular Calibration
Regular calibration of H2S monitors is not just a best practice—it is a fundamental aspect of occupational safety. Here are several reasons why it is crucial:
- Accurate Measurements: Calibration ensures that H2S monitors deliver accurate readings, which is vital for making informed safety decisions.
- Compliance with Regulations: Many industry standards and regulations require regular calibration of monitoring equipment to ensure workplace safety.
- Protecting Lives: Accurate calibration can prevent exposure to dangerous levels of H2S, protecting workers from serious health risks, including respiratory issues and death.
- Equipment Longevity: Regular calibration can help prolong the life of the monitoring equipment, saving money on replacements and repairs.
How Often Should H2S Monitors Be Calibrated?
The frequency of calibration can depend on several factors such as:
- Type of environment in which the monitor is used (hazardous vs. non-hazardous)
- Manufacturer's recommendations
- The device's usage patterns (how often it's used and under what conditions)
Generally, it is advisable to calibrate H2S monitors at least every six months, but high-risk environments may require more frequent checks.
Steps to Calibrate H2S Monitors
The calibration process typically involves the following steps:
- Preparation: Ensure the monitor is clean and free from contaminants.
- Test Gas Preparation: Obtain a calibration gas that contains a known concentration of H2S.
- Connect the Monitor: Attach the monitor to a calibration gas source, using appropriate adapters to ensure a secure connection.
- Introduce Calibration Gas: Gradually introduce the calibration gas into the monitor’s sensor, observing the display.
- Adjust Readings: If the readout does not match the known concentration, adjust the monitor settings accordingly.
- Document the Calibration: Record the date, gas concentration, and any adjustments made for future reference.
The Calibration Equipment You Need
High-quality calibration equipment is crucial for effective calibrations. Here are essential tools you might need:
- Calibration Gas Cylinder: Ensure you have a reliable supply of calibration gas with the correct concentration of H2S.
- Flow Regulator: This device controls the flow of calibration gas to the sensor, preventing damage from high pressure.
- Calibration Kit: Includes necessary components such as adapters and tubing for connecting the monitor to the gas cylinder.
- Personal Protective Equipment (PPE): Always use appropriate PPE when handling H2S or during calibration processes.
Best Practices for H2S Monitor Calibration
To ensure the most effective calibration of H2S monitors, follow these best practices:
- Always Follow Manufacturer Guidelines: Each H2S monitor may have specific calibration procedures that must be followed closely.
- Keep a Calibration Log: Maintain a detailed record of calibration dates, results, and any maintenance performed on the monitor.
- Train Personnel: Ensure that staff responsible for calibration are properly trained and understand the procedures and the importance of accuracy.
- Inspect Equipment Regularly: Check monitors for signs of wear or damage and perform maintenance as needed.
Conclusion
In industries where H2S is a risk, proper calibration of H2S monitors plays a vital role in ensuring safety and compliance with regulations. By committing to rigorous calibration schedules, utilizing best practices, and employing the right equipment, companies can protect their workforce while maintaining operational efficiency.
For more information on environmental safety and technological training, visit h2sonlinetraining.com. Investing in your team's education and understanding of H2S monitor calibration can lead to safer workplaces and improved employee morale.