The Essential Role of Automotive Plastic Molding in Modern Manufacturing
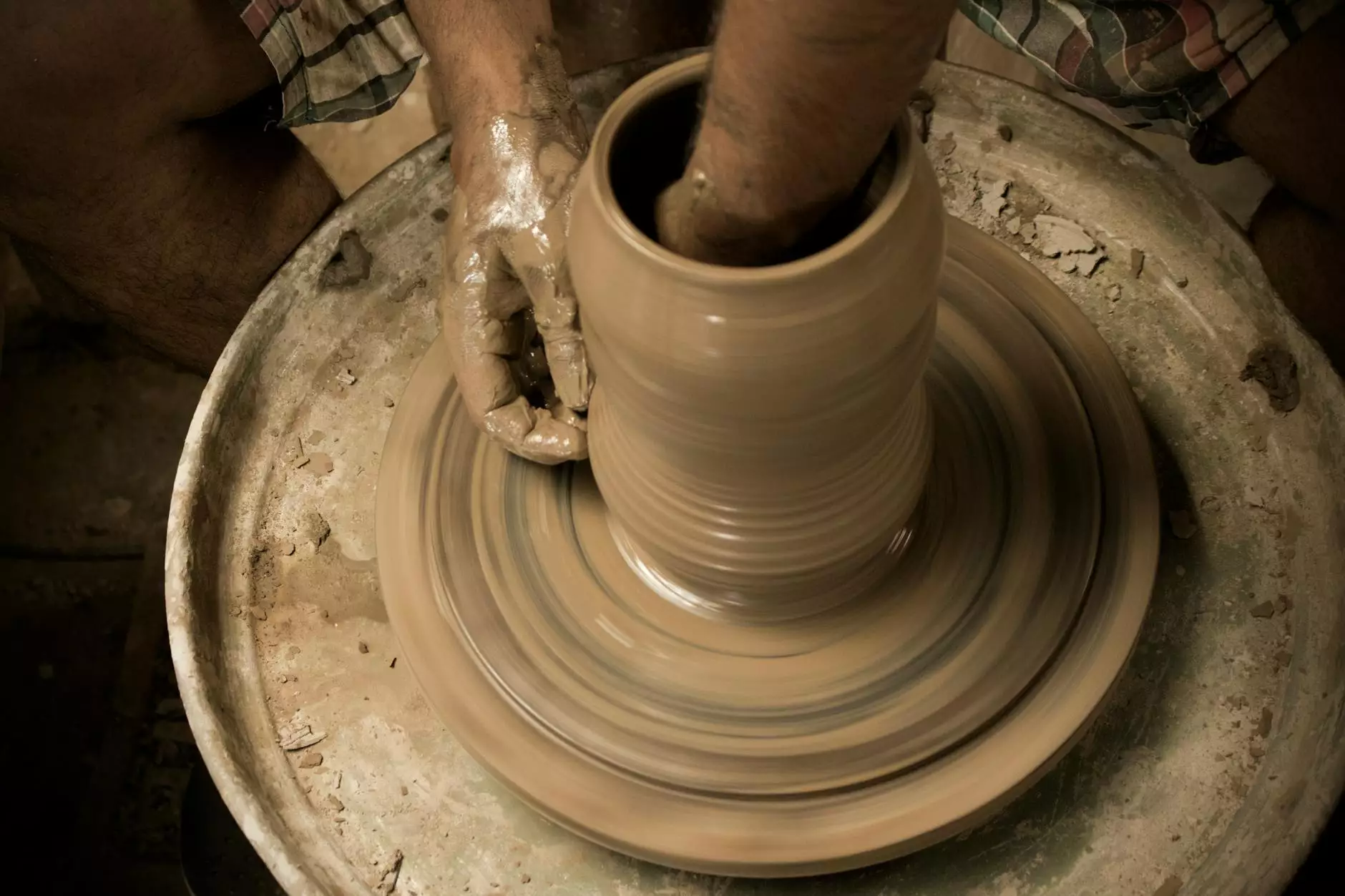
In the fast-paced world of manufacturing, particularly in the automotive sector, automotive plastic molding has emerged as an invaluable process. As industries evolve, the demand for lightweight, durable, and cost-effective materials has never been greater. This article aims to delve into the intricacies of automotive plastic molding, highlighting its significance, methodologies, and future potential within the realm of automotive manufacturing.
Understanding Automotive Plastic Molding
Automotive plastic molding refers to the process of shaping plastic materials into specific forms used in automotive components. This manufacturing technique employs various methods, including injection molding, blow molding, and rotational molding. Each method serves unique purposes but shares the common goal of producing high-quality, consistent parts that meet strict automotive standards.
The Benefits of Automotive Plastic Molding
The advantages of utilizing automotive plastic molding are numerous. Here are some of the key benefits:
- Weight Reduction: Plastic components are significantly lighter than their metal counterparts, leading to improved fuel efficiency.
- Design Flexibility: The ability to mold complex shapes provides designers with immense flexibility, allowing for innovative product development.
- Cost-Effectiveness: The high-speed production cycle of plastic molding reduces manufacturing costs significantly.
- Corrosion Resistance: Plastics are inherently resistant to corrosion, enhancing the longevity of automotive parts.
- Customizable Properties: Different additives can be mixed into plastics, giving manufacturers the ability to tailor physical properties to suit specific applications.
Key Processes in Automotive Plastic Molding
Understanding the main processes involved in automotive plastic molding is crucial for manufacturers aiming to optimize production. Let's explore the primary methods:
1. Injection Molding
Injection molding is perhaps the most widely utilized technique in automotive plastic molding. This process involves injecting heated, molten plastic into a mold, where it cools and solidifies into the desired shape. Key benefits include:
- High Efficiency: Injection molding is capable of producing thousands of identical parts quickly.
- Low Waste: Excess material can often be recycled, minimizing waste.
- Precision: The process allows for tight tolerances, critical for automotive applications.
2. Blow Molding
While not as commonly associated with automotive applications, blow molding is used to produce hollow plastic parts, such as fuel tanks. This method involves air being blown into a soft plastic tube, allowing it to conform to the shape of the mold. Its advantages include:
- Cost-Effectiveness: Ideal for high-volume production runs.
- Lightweight Structures: Creates strong, lightweight components crucial for automotive efficiency.
3. Rotational Molding
Primarily used to produce large, hollow components like storage tanks and certain vehicle parts, rotational molding helps to maintain consistent wall thicknesses and enhance structural integrity. Benefits include:
- Large Parts Production: Suitable for creating large-sized hollow components.
- Minimal Waste: Produces virtually no waste material during manufacturing.
The Role of Design in Automotive Plastic Molding
Effective design plays an indispensable role in the automotive plastic molding process. Engineers and designers must consider the following factors to ensure the molding process is successful:
- Material Selection: The choice of plastic greatly affects the performance, durability, and overall quality of the final product.
- Mold Design: Well-designed molds facilitate efficient production and contribute to product quality.
- Post-Processing: Consideration of any required finishing processes, like painting or plating, is crucial to meet aesthetic and functional requirements.
Applications of Automotive Plastic Molding
The applications of automotive plastic molding are vast and varied. Here are some notable uses:
Interior Components
From dashboards to door panels, plastic molding allows for the production of lightweight yet durable interior components that enhance both the aesthetic and comfort of vehicles.
Exterior Components
Many exterior elements, including bumpers, fenders, and trim, are commonly produced using automotive plastic molding. These parts are designed to endure harsh conditions while providing style and functionality.
Functional Components
Functional automotive parts, such as clips, brackets, and housings for lights and sensors, benefit from the precision and customization afforded by plastic molding. This ensures that critical components perform effectively and reliably.
The Future of Automotive Plastic Molding
The future of automotive plastic molding appears bright as technology continues to advance. Innovations such as 3D printing and smart materials are beginning to reshape manufacturing processes, offering exciting opportunities for efficiency and customization.
Sustainability and Recycling
As the automotive industry aims for greater sustainability, the focus on recyclable materials and processes that minimize environmental impact is becoming paramount. Automotive plastic molding is evolving to include bioplastics and other sustainable materials that align with global recycling initiatives.
Smart Manufacturing
The integration of smart technologies into plastic molding processes, such as IoT (Internet of Things) and AI (Artificial Intelligence), can lead to enhanced monitoring, scheduling, and predictive maintenance. These advancements promise to improve operational efficiency and reduce downtime.
Choosing the Right Partner for Automotive Plastic Molding
Selecting the right manufacturing partner is critical in the realm of automotive plastic molding. When evaluating potential suppliers, consider the following:
- Experience: Look for companies with a proven track record in automotive applications.
- Technology: Ensure they utilize modern technologies and processes to maintain high-quality production standards.
- Customization: Choose a partner capable of providing tailored solutions to meet specific project needs.
- Regulatory Compliance: Verify that they adhere to industry regulations and standards.
Conclusion
In conclusion, automotive plastic molding is not merely a process; it is a critical driver of innovation and efficiency in the automotive industry. With its numerous benefits, evolving technologies, and a focus on sustainability, it is clear that automotive plastic molding will continue to play a pivotal role in the future of manufacturing. By investing in this technology and materials, manufacturers like DeepMould.net are positioning themselves at the forefront of an industry poised for growth and advancement.
As the automotive landscape changes, the ability to adapt and harness the full potential of automotive plastic molding will determine the success of businesses in this vibrant sector.