The Importance of H2S Monitor Calibration
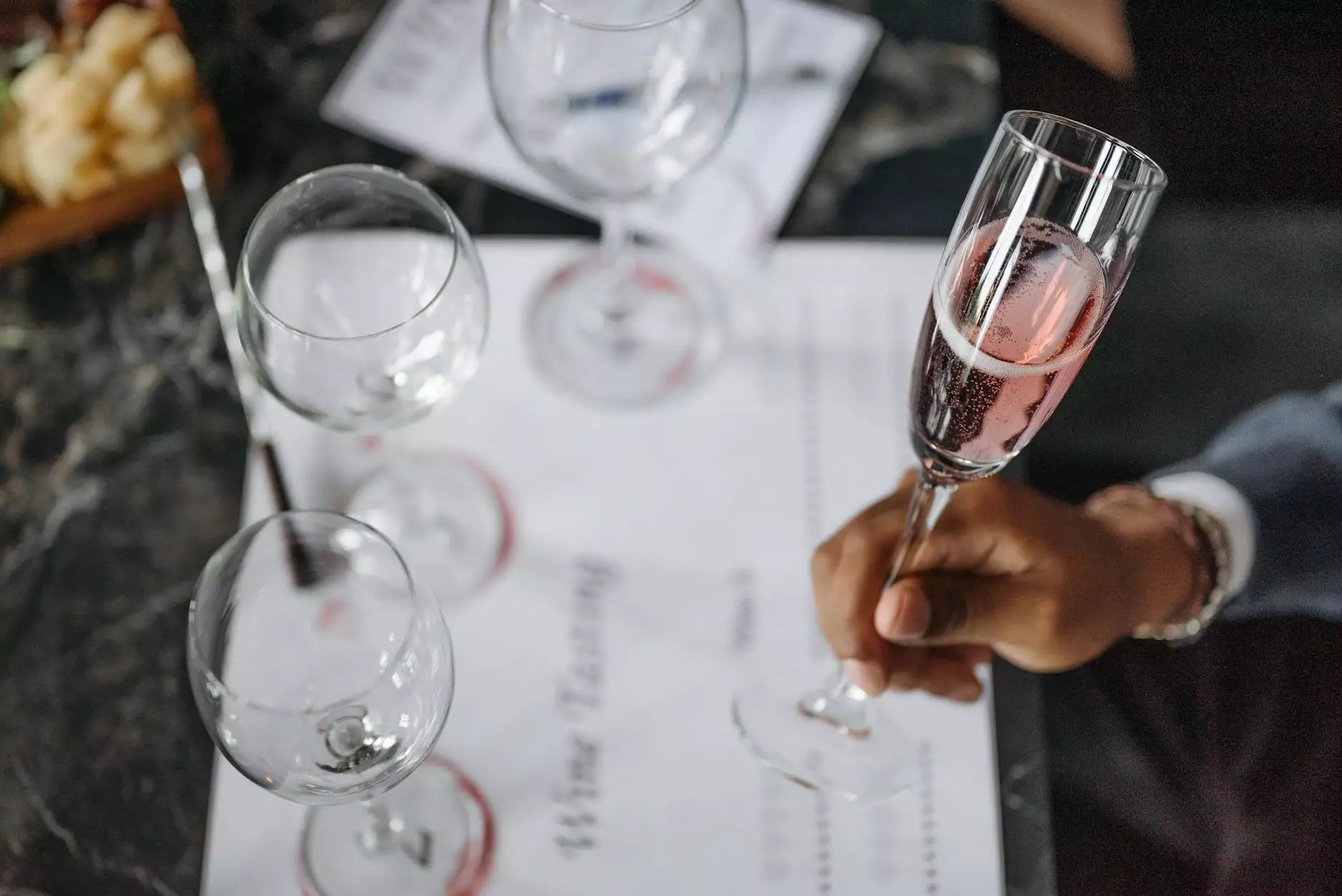
Hydrogen sulfide (H2S) is a highly toxic gas that poses a serious risk to workers in various industries, including oil and gas, mining, and wastewater treatment. As such, the proper calibration of H2S monitors is essential for ensuring workplace safety and compliance with regulatory standards. In this article, we will delve into the significance of H2S monitor calibration, the best practices for maintaining these systems, and how H2S Online Training can assist organizations in achieving their safety and training goals.
Understanding H2S and Its Risks
H2S is a colorless gas known for its distinct smell of rotten eggs. It is flammable and can be extremely hazardous to human health, causing respiratory issues, unconsciousness, and even death in high concentrations. Given these dangers, monitoring H2S levels in environments where it may be present is crucial.
Health Effects of H2S Exposure
- Low Concentrations (0-10 ppm): Irritation of the eyes, nose, and throat.
- Moderate Concentrations (10-50 ppm): Headaches, dizziness, nausea, and loss of sense of smell.
- High Concentrations (50-100 ppm): Respiratory distress, unconsciousness.
- Very High Concentrations (above 100 ppm): Immediate life-threatening health effects.
Due to the potential for serious health risks, it is imperative that workers have access to accurate and reliable H2S monitoring equipment. This is where the calibration of H2S monitors becomes vital.
What is H2S Monitor Calibration?
Calibration is the process of adjusting the precision of a device to ensure its measurements accurately reflect the true concentration of a given substance. In the case of H2S monitors, calibration involves comparing the monitor’s readings to a known standard and making adjustments as necessary.
Why Calibration is Critical
Here are some reasons why H2S monitor calibration is crucial:
- Accuracy: Regular calibration ensures that the monitor provides accurate readings of H2S levels, which is critical for worker safety.
- Compliance: Regulatory bodies often require regular calibration of monitoring equipment to ensure compliance with safety standards.
- Early Detection: Accurate readings enable early detection of H2S leaks, allowing for swift action to mitigate risks.
- Reliability: A calibrated monitor can instill confidence in users, knowing that they can rely on the device during emergencies.
Best Practices for H2S Monitor Calibration
To ensure that H2S monitors remain accurate and reliable, organizations should adhere to several best practices regarding calibration.
1. Establish a Calibration Schedule
Organizations should develop a calibration schedule based on the manufacturer’s recommendations, regulatory requirements, and the frequency of use. Regular checks can prevent inaccuracies and ensure reliable monitoring.
2. Utilize Proper Calibration Gases
It is essential to use the correct gases for calibration. Manufacturers typically specify the gases and concentrations that should be used. Always follow the manufacturer's guidelines to ensure accuracy.
3. Train Staff Effectively
Proper training for staff members is crucial. Employees should understand how to calibrate the devices accurately and recognize the importance of maintaining calibrated equipment. Programs like those offered by H2S Online Training can be invaluable for achieving this goal.
4. Document Calibration Procedures
Documentation is key in maintaining compliance and improving safety protocols. Every time a monitor is calibrated, the details should be logged, including the date, results, and any adjustments made.
5. Test the Equipment Regularly
In addition to scheduled calibrations, routine testing of H2S monitors monthly or before use in high-risk environments can catch any issues early.
Common Challenges in H2S Monitor Calibration
While the importance of calibration is clear, organizations may face challenges in implementing effective practices. These can include:
- Resource Allocation: Allocating time and budget for regular calibrations can be a challenge for some organizations.
- Equipment Availability: Ensuring that the necessary calibration equipment and gases are available when needed may require planning.
- Employee Turnover: High turnover may result in a lack of trained personnel capable of conducting calibrations.
Overcoming these challenges requires a proactive approach to training and scheduling, as well as a commitment to workplace safety standards.
The Role of H2S Online Training in Calibration
Proper training is vital for both safety and compliance. H2S Online Training, found at h2sonlinetraining.com, offers a comprehensive curriculum designed to educate users on the intricacies of H2S safety, including calibration protocols. Key features of their program include:
- Interactive Online Modules: Users can learn at their own pace with engaging multimedia content.
- Expert Instructors: The program is developed by professionals with real-world experience in H2S monitoring and safety practices.
- Certification: Participants can earn certifications that are vital for career advancement and compliance.
Conclusion
In conclusion, H2S monitor calibration is not merely a procedural step, but a vital component in ensuring the safety and health of workers exposed to this harmful gas. By adhering to best practices, overcoming challenges, and investing in proper training, organizations can significantly reduce the risks associated with H2S exposure. Embracing a culture of safety through education and effective monitoring will not only protect individuals but also enhance the overall efficiency of operations.
Visit H2S Online Training today to learn more about essential training programs that can equip your workforce with the knowledge they need to manage H2S hazards effectively.