Revolutionizing Manufacturing with Plastic Molding Electrical
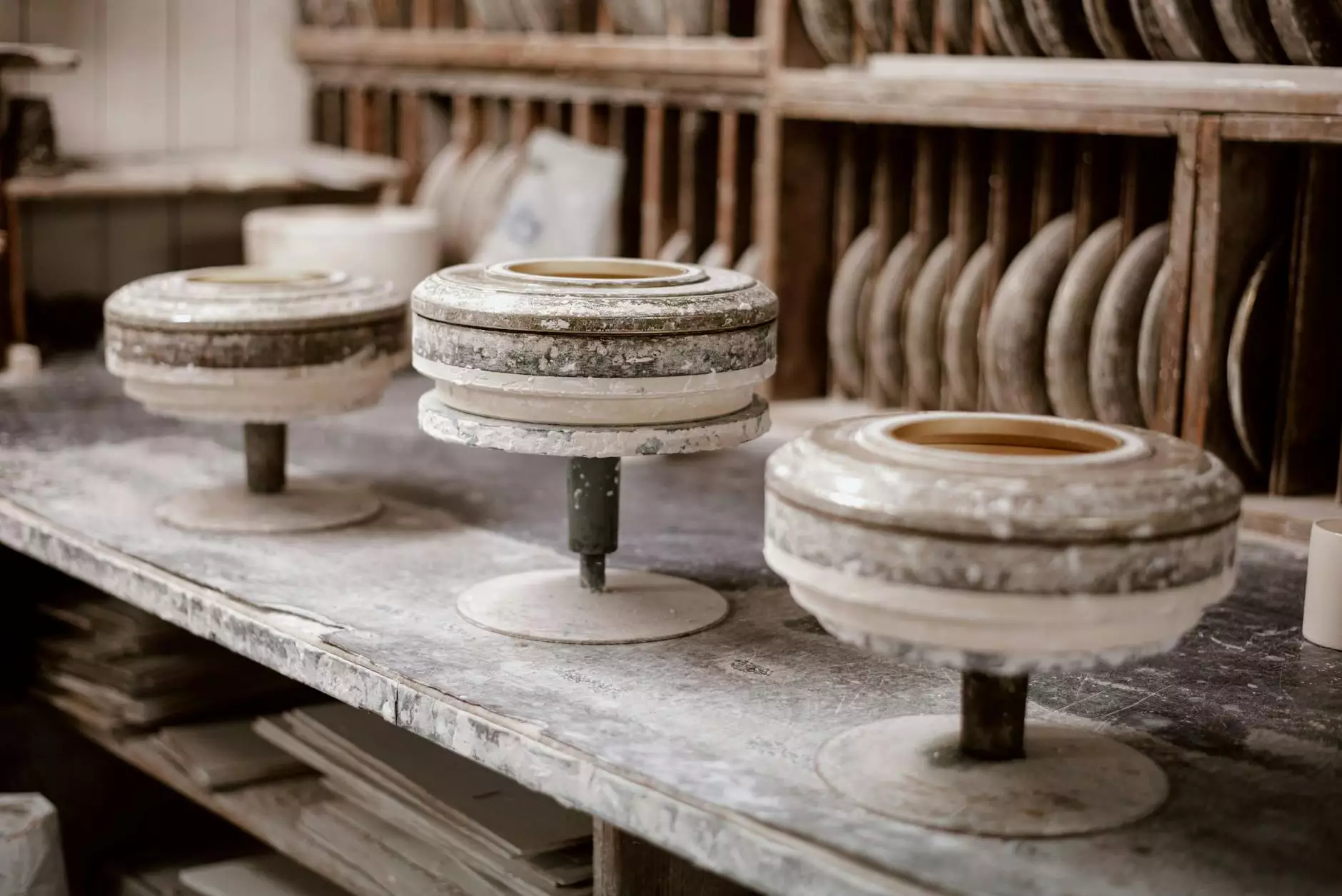
In the realm of modern manufacturing, plastic molding electrical processes stand as a cornerstone of innovation and efficiency. This article delves into the intricacies of plastic molding in electrical applications, highlighting its significance in various industries and the future prospects it holds.
Understanding Plastic Molding Electrical
Plastic molding is a technique used to produce various components and products by injecting molten plastic into molds. The term plastic molding electrical refers specifically to this process when it involves creating parts that will be used in electronic and electrical devices. This technology has transformed the way manufacturers approach production, enabling them to create intricate designs, reduce waste, and enhance performance.
Why Plastic Molding is Essential in the Electrical Industry
Plastic molding isn't just a manufacturing method; it's an essential technology in the electrical industry. Here are some reasons why:
- Design Flexibility: Plastic molding allows for the creation of complex shapes and sizes that are often impossible with traditional manufacturing techniques.
- Cost Efficiency: Mass production of electrical components through plastic molding significantly lowers per-unit costs, making it an attractive option for manufacturers.
- Weight Reduction: Plastic components are often lighter than their metal counterparts, contributing to lighter and more energy-efficient products.
- Durability: High-quality plastics can offer excellent resistance to corrosion, heat, and impact, making them ideal for electrical applications.
- Customization: Manufacturers can easily customize specifications to meet various electrical standards and requirements.
The Process of Plastic Molding Electrical
The process of plastic molding involves several key steps, each of which plays a critical role in the production of electrical components:
1. Material Selection
The first step involves selecting the right type of plastic. Common materials include: - Polycarbonate (PC): Known for its high impact resistance and optical clarity. - Acrylonitrile Butadiene Styrene (ABS): Valued for its strength and toughness. - Polypropylene (PP): Ideal for applications requiring chemical resistance.
2. Mold Design
Mold design is crucial to achieving the desired shape and functionality of the final product. Advanced computer-aided design (CAD) software is often used to create precise mold designs that will ensure consistency in production.
3. Injection Molding
During this phase, the chosen plastic is heated until it melts and then injected into the mold. The cooling time depends on the thickness and complexity of the mold.
4. Finishing Processes
After cooling, the molded parts may undergo additional finishing processes, such as trimming, sanding, or painting, to meet aesthetic and functional requirements.
Applications of Plastic Molding Electrical
The applications of plastic molding electrical are vast and varied. Here are some of the key areas where this technology is making a significant impact:
1. Consumer Electronics
From smartphone casings to laptop components, plastic molding is integral in producing lightweight yet durable parts that are essential for functionality and style.
2. Automotive Industry
Modern vehicles rely heavily on electrical systems, making plastic molding pivotal in creating components such as wiring harnesses, connectors, and interior trim pieces.
3. Medical Devices
The medical field requires precision and reliability, which is why plastic molded parts are often used in devices like diagnostic instruments, housings for electronic medical equipment, and more.
4. Industrial Applications
In industrial settings, plastic molding is used to create housing for various electrical controls, circuit boards, and other essential components that enhance operational efficiency.
The Environmental Impact of Plastic Molding Electrical
As the push for sustainable practices grows, the plastic molding electrical industry is adapting to meet environmental concerns:
- Recyclable Materials: Many modern plastics can be recycled, reducing waste and encouraging a circular economy.
- Energy Efficiency: Innovations in molding technology have led to processes that consume less energy during production.
- Reduced Material Waste: Precision molding processes minimize waste, utilizing only the necessary amount of material.
Future Trends in Plastic Molding Electrical
Looking ahead, several trends are shaping the future of plastic molding electrical:
1. Adoption of Bioplastics
With an increasing emphasis on sustainability, bioplastics made from renewable resources are gaining traction, offering environmentally friendly alternatives to traditional plastics.
2. Smart Technologies and IoT
The Internet of Things (IoT) is driving demand for more sophisticated components that integrate smart technology, creating opportunities for innovative plastic molded products.
3. Advanced Automation and Robotics
Automation in the molding process is enhancing precision while reducing production times, lessening labor costs and increasing overall efficiency.
4. Customization and Rapid Prototyping
As industries increasingly demand unique solutions, rapid prototyping technologies, like 3D printing, combined with traditional molding are becoming common practice for quick iterations and customization.
Conclusion
In summary, plastic molding electrical represents a dynamic intersection of technology, innovation, and manufacturing. Its flexibility, cost-effectiveness, and capacity for customization make it indispensable across multiple sectors. As industries continue to evolve, embracing sustainability and advanced technologies, plastic molding will undoubtedly play a vital role in shaping the future of electrical components and systems.
For businesses looking to leverage these advancements, aligning with a proficient *metal fabricators* partner like DeepMould.net can unlock new possibilities and drive success in the competitive market.